Kommentar von Andreas Gladis : Digitale Zwillinge allein machen nicht glücklich
Der Maschinenbau ist eine der deutschen Vorzeigebranchen. Seine Produkte werden in der ganzen Welt geschätzt, weil sie innovativ und von hoher Qualität sind. Sie entstehen in komplexen Produktionsprozessen, die teilweise mehr als zehntausend Arbeitsschritte umfassen und in denen eine Vielzahl von Rohstoffen und Bauteilen unter Einsatz spezialisierter Fertigungsanlagen und qualifizierter Mitarbeiter zusammengefügt wird. Das feine Geflecht aus Prozessen mit all ihren Zusammenhängen und Abhängigkeiten vermag allerdings schon lange kein Mensch mehr zu überblicken. Selbst mit digitalen Lösungen wie ERP-Systemen und Excel, auf die die meisten Maschinenbauer setzen, gelingt es meist nicht, für jeden Auftrag alle notwendigen Ressourcen zum richtigen Zeitpunkt bereitzustellen. Produktionsverzögerungen sind daher an der Tagesordnung und die Mitarbeiter regelmäßig mit Feuerwehrmaßnahmen beschäftigt.
Zwar arbeitet die Branche häufig mit Überbeständen und Pufferzeiten, doch das ist weder effizient noch geeignet, umfangreichere Störungen zu überbrücken – das haben die vergangenen Monate gezeigt. Unterbrochene Lieferketten aus Fernost, Unwetter in Mitteleuropa und die Auswirkungen einer globalen Pandemie bringen früher oder später jede noch so sorgfältig erstellte Planung aus dem Tritt. Zudem verzeichnet der Maschinenbau seit einiger Zeit wieder zweistellig wachsende Auftragszahlen1, weil Kunden ihre Bestellrückstände aufholen oder neue Investitionsprojekte planen. Das führt zu kurzfristigen Aufträgen, die eingeschoben und schnell abgearbeitet werden müssen, wenn sie von wichtigen Kunden kommen oder ein großes Volumen haben. Auch deshalb treibt der Maschinenbau inzwischen seine Digitalisierung mit Nachdruck voran: Er strebt insbesondere nach Verbesserungen beim Produktionsmanagement und der Produktionsplanung, um eine höhere Termintreue, kürzere Durchlaufzeiten und Kosteneinsparungen zu erreichen.
Digitale Abbilder realer Objekte und Abläufe
Auf großes Interesse stoßen in der Branche seit geraumer Zeit digitale Zwillinge. Die digitalen Abbilder von Maschinen, Prozessen, Produkten oder auch ganzen Fertigungsstraßen und einzelnen Aufträgen liefern detaillierte Einblicke in die Produktion. Ohne sich in die Fertigungshalle begeben oder Informationen aus verschiedenen Systemen zusammensuchen zu müssen, sehen die Verantwortlichen in Echtzeit, wo eine Maschine heiß läuft oder nicht ausgelastet ist, wo sich Teile stauen oder Abläufe stocken. Sie können mit einem Blick den Status von Aufträgen überprüfen und ermitteln, bei welchen eine termingerechte Fertigstellung in Gefahr ist und wo die Ursachen dafür liegen.
Damit liefern digitale Zwillinge eine bislang unerreichte Transparenz, doch zu einer resilienteren und agileren Fertigung tragen sie kaum bei. Denn was passiert, wenn sich ein Lieferant verspätet oder ein Eilauftrag eintrifft? Dann stehen Planer weiterhin vor der großen Herausforderung, die vorhandenen Rohstoffe und Bauteile sowie die verfügbaren personellen und maschinellen Produktionskapazitäten umzuplanen. Das kostet viel Zeit und führt nur selten zu Ergebnissen, bei denen alle Ressourcen optimal genutzt und sämtliche Aufträge bestmöglich erfüllt werden.
Ein digitaler Zwilling allein ist damit für die Produktionsplanung ähnlich unzureichend wie eine umfassende digitale Straßenkarte bei der Routenplanung. Eine solche Karte würde, wenn sie auch Baustellen, Verkehrsflüsse und Wetterbedingungen anzeigt, einen hervorragenden Überblick liefern, wo Verspätungen drohen. Mit einigem Aufwand könnten vorab sogar Routen ausgearbeitet werden, die bis dahin bekannte Staus aussparen. Doch für eine schnelle und flexible Neuplanung der Routen, wenn im Laufe der Fahrt neue Behinderungen auftauchen, braucht es smarte Navigationsfunktionen – vor allem wenn die Fahrzeugflotte groß ist und je nach Ladung entweder kurze Fahrzeiten oder niedriger Spritverbrauch höchste Priorität haben.
Algorithmen optimieren die Planung
Das smarte Navi im Auftrags- und Prozessgeflecht, das digitale Zwillinge in der Produktion abbilden, sind APS-Systeme (Advanced Planning and Scheduling). Sie nutzen mathematische Modelle, um einen realistischen und optimierten Produktionsplan zu erstellen, der alle Ressourcen, Kapazitäten und Termine berücksichtigt.
Bei Störungen wie Materialengpässen, Maschinenausfällen oder Terminverschiebungen spielen die Algorithmen in kürzester Zeit unzählige Szenarien durch und passen den Produktionsplan dynamisch an. Sie legen fest, welche Aufträge und Arbeitsschritte nun Priorität haben und welche Mitarbeiter und Maschinen die Arbeiten übernehmen. Einige Planungs- und Dispositionsentscheidungen treffen die Algorithmen automatisch und ermöglichen damit Reaktionen nahezu in Echtzeit. Andere Entscheidungen beschleunigen sie, indem sie den Planern Handlungsoptionen aufzeigen und Empfehlungen liefern.
Zwar können APS-Systeme keine Produktionsstörungen vorhersagen oder verhindern, aber deren Auswirkungen minimieren, indem sie bei schnellen und optimierten Reaktionen unterstützen. Dabei finden sie auch Lösungen, auf die Menschen häufig nicht kommen, weil sie ihrer Intuition widersprechen – etwa, wenn sie einzelne Aufträge gezielt verzögern, um insgesamt mehr Aufträge fristgerecht fertigzustellen.
Die Basis sind genaue Daten
Die Datenbasis für solche intelligenten Planungswerkzeuge liefert das bestehende ERP-System. Zudem ist eine Betriebsdatenerfassung (BDE) sinnvoll, um Termine, Ressourcen und den Status von Aufträgen im Blick zu behalten. Digitale Zwillinge stellen dieses Gesamtbild dann lediglich dar, während APS-Systeme die Planung optimieren und kontinuierlich anpassen.
Auf diese Weise machen Maschinenbauer ihre Produktion unempfindlich gegenüber kleinen und großen Störungen, verkürzen ihre Fertigungszeiten und halten Lieferzusagen besser ein. Zudem senken sie ihre Kosten erheblich, weil sie mit geringeren Reservebeständen auskommen und seltener Teile kurzfristig beschaffen müssen. Bisweilen tun sich sogar unerwartete Einsparmöglichkeiten auf, beispielsweise wenn sich durch die optimierte Planung regelmäßige Staus vor einer Maschine auflösen und die Neuanschaffung einer zweiten Maschine überflüssig machen. Ganz so, als würde das Navi aus dem Kartenbeispiel die Routen und Fahrzeiten soweit optimieren, dass das Unternehmen mit einer kleineren Fahrzeugflotte auskommt. Eine digitale Karte beziehungsweise ein digitaler Zwilling allein kann das nicht leisten.
Letztlich lernen Unternehmen durch digitale Zwillinge und intelligente Planungstools mehr über sich selbst und ihre Prozesse. Sie dürfen sich allerdings nicht nur darauf beschränken, neue Daten zu erfassen und den Ist-Zustand eins zu eins sichtbar zu machen, sondern müssen all dies für Problemlösungen und Prozessverbesserungen nutzen. Soll es also wirklich nur die digitale Landkarte mit allen Verkehrsmeldungen sein oder doch lieber auch das Navi, das agil und bei Bedarf eine optimale neue Route berechnen kann?
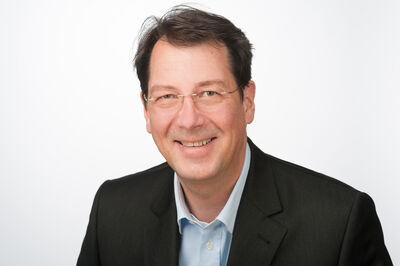