Yaskawa : Komplexe Handlingaufgabe als Einstieg in die Robotik
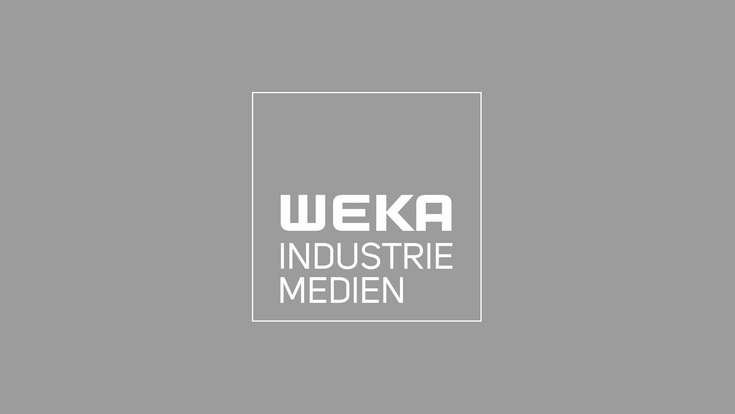
Ob Automobil- und Zulieferindustrie, Maschinenbau, Elektronikfertigung, Beschlaghersteller, Feinmechanik oder Uhrenindustrie – Montage- und Automatisierungstechnik des sächsischen Sondermaschinenbauers Kleinig engineering GmbH & Co. KG kommt in vielen Branchen zum Einsatz. Ein Grund für diesen Markterfolg: Das seit 1998 in Großpösna bei Leipzig aktive Unternehmen deckt den Anlagenbau in seiner ganzen Breite ab und vereint Entwicklung, Konstruktion, Elektroplanung, Programmierung, Fertigung und Service unter einem Dach.
Komplexe Aufgabenstellung
So waren die Experten von Kleinig engineering auch gut gerüstet, als sie 2019 die Anfrage eines Kunden aus der Automotive-Branche erreichte: Ein bestehender Montageprozess sollte automatisiert werden, um auf diesem Weg zum einen Stückzahlen und Durchsätze zu erhöhen und zum anderen die Anzahl der erforderlichen Werker zu reduzieren.
Konkret ging es dabei um die Montage von Gummi-Metall-Lagern für Querlenker und Schwenklager. Und damit um eine sehr anspruchsvolle Automatisierungsaufgabe, denn bei diesen Fahrwerkskomponenten handelt es sich um Schmiedeteile mit teilweise großen Fertigungstoleranzen. Diese Spielräume schließen sich konstruktionsbedingt erst im weiteren Fertigungsprozess und erfordern bis dahin eine hohe Flexibilität im Handling. Darüber hinaus liegt die Greifposition auf unbearbeiteten Flächen, was zusätzliche Anforderungen an die Effektoren stellt.
Zur Umsetzung dieser sehr speziellen Aufgabenstellung wurden verschiedene Konzepte diskutiert, wobei die Konstrukteure von Kleinig engineering eine roboterbasierte Lösung favorisierten. „Allerdings hatte der Kunde anfangs ,Bauchschmerzen‘ beim Thema Robotik“, wie sich Prokurist und Vertriebsleiter Tobias Franz erinnert. Diese Skepsis war nicht nur in der Komplexität des Montageprozesses begründet, sondern auch darin, dass das Unternehmen bisher noch keine Roboter eingesetzt hatte und dementsprechend nicht auf eigene Kompetenzen und Erfahrungen in diesem Bereich zurückgreifen konnte.
Dass sich der Kunde letztlich doch für die roboterbasierte Option – und damit für einen Einstieg in die Robotik insgesamt – entschied, lag an dem überzeugenden, SPS-basierten Anlagenkonzept, mit dem Kleinig engineering ihn überzeugte. Dieses hat sich inzwischen bewährt als flexible Montagelösung zur Produktion von Losgröße 1 ohne Rüstaufwand.
Montagezelle als Komplettlösung
Die Komplettlösung kombiniert zwei Montagestationen, eine für das Gummi-Metall-Lager und eine für die Buchse. In jeder arbeitet ein Industrieroboter. Beide Bearbeitungsschritte können parallel durchgeführt werden. Verkettet sind die beiden Stationen durch ein Umlaufsystem, auf dem für alle Bauteilvarianten geeignete Universalwerkstückträger durch die Zelle transportiert werden. Je nach Bauteil beträgt die Bearbeitungszeit rund eine Minute. Für die Bedienung der kompletten Zelle reicht ein einziger Mitarbeiter aus. Die Zuführung bzw. Einschleusung der zu montierenden Einzelteile in die Montagezelle erfolgt an einer Werkerstation, wo sie manuell auf den Werkstückträger aufgelegt werden. Anschließend übernehmen die beiden Roboter automatisch das komplette Bauteilhandling und sämtliche Bearbeitungsschritte.
Diese umfassen im Einzelnen: in der Montagestation für Gummi-Metall-Lager das Einlegen des Querlenker-Bauteil in die Montagevorrichtung, den Ausgleich von Bauteiltoleranzen, die aktive Ausrichtung der Fügeachse im Bauteil, das Handling von zwei Gummi-Metall-Lagern zur Benetzung mit Gleitmittel und die Platzierung auf dem Fügewerkzeug, die Montage der Gummi-Metall-Lager auf Einbaumaß des Querlenkers durch zwei servomotorische Fügeeinheiten (Kistler) und die optische Abschlussprüfung mit Sensoren der Firma Keyence. Anschließend werden die montierten Querlenker für den Weitertransport auf dem Werkstückträger abgelegt.
[Bild:4]
In der anschließenden Montagestation für die Buchse übernimmt der Roboter: die Platzierung der Buchse auf dem Einpresswerkzeug, die Positionierung des Querlenkers bzw. Schwenklagers in die Montagevorrichtung, Montage der Buchse durch eine Fügeachse ohne öffnen des Greifsystems, das Handling des Bauteil zur Beschriftung mittels Klebe-Label, Gut-/Schlechtteil-Ablage auf Werkstückträger oder NIO-Box sowie den Weitertransport des Werkstückträgers zur Entnahme des fertig montierten Bauteils außerhalb der Montageanlage.
An beiden Robotern ermöglichen Doppelgreifer das Handling der unterschiedlichen Komponenten ohne Greiferwechsel, was höhere Taktzeiten erlaubt. Auch die Umrüstung bei einem Bauteilwechsel von Querlenker auf Schwenklager bzw. umgekehrt erfolgt sehr zeitsparend durch den Einsatz eines Schnellwechselsystems (Schunk Typ SWK) zum automatischen Greiferwechsel.
Entscheidung für Handlingroboter Motoman GP25
Bei der Auswahl der geeigneten Roboter stand für die Konstrukteure bei Kleinig engineering die Entscheidung für einen Motoman-Modell von Anfang an fest: „Wir haben uns schon seit Jahren auf Yaskawa festgelegt und sind auch sehr zufrieden mit dieser Entscheidung“, betont David Kleinig, Prokurist und Leiter Steuerungstechnik, und nennt zum Beispiel die komfortable Inbetriebnahme und den schneller Telefonsupport als Gründe.
Aufgrund ihrer spezifischen Reichweite und Leistungsdaten boten zwei Motoman GP25 mit je 25 kg Tragkraft die optimale Lösung für die aktuelle Aufgabenstellung: „GP“ steht für „General Purpose“ und damit für vielfältige Einsatzmöglichkeiten. Die 6-Achser sind damit auch ideal für das Bauteilhandling und Montageaufgaben geeignet. Bei schwierigen Einlegesituationen ermöglicht es die sogenannte Servofloat-Option, die Roboterachsen weich zu schalten, um Bauteiltoleranzen auszugleichen.
Wie alle Modelle der Motoman GP-Serie ist auch der GP25 in der hohen Schutzklasse IP67 ausgeführt und damit besonders geschützt gegen Eindringen von Flüssigkeiten und Stäuben. Er lässt sich also auch unter rauen Arbeitsbedingungen einsetzen und sehr leicht reinigen. Der Roboter kann zudem ohne Einschränkungen in beliebiger Einbaulage arbeiten. Roboterkabel lassen sich entweder seitlich oder durch den Sockel hindurch einführen. Die integrierte Medienversorgung in den Achsen optimiert den Aufbau von Greifern und sorgt für höchste Zuverlässigkeit im späteren Betrieb.
Nicht zuletzt sorgt die kompakte Hochleistungssteuerung YRC1000 für eine einfache Bedienung und Programmierung. Dafür kann entweder das klassische Programmierhandgerät oder das innovative Smart Pendant verwendet werden.
[Bild:2]
Steuerungskonzept
Als Besonderheit der aktuellen Anlage sind die beiden Roboter direkt über SPS-Funktionsbausteine in ein übergeordnetes Steuerungskonzept eingebunden. Dieses umfasst zwei Maschinensteuerungen: eine SPS zur Steuerung der Gesamtanlage und eine weitere SPS zur Integration der komplexen Roboterbewegungen. Bedient wird die Anlage zentral auf einem Mobile-Panel (HMI).
Die eigentliche Anbindung der Robotersteuerungen an die SPS erfolgt über die Softwareschnittstelle MotoLogix. Damit lassen sich Motoman-Roboter von Yaskawa im gängigen IEC-61131-Umfeld schnell und unkompliziert über die SPS programmieren und steuern. Das Spektrum unterstützter Plattformen umfasst alle gängigen Standards. Die Konstrukteure von Kleinig engineering nutzen Controller von Siemens und dementsprechend Profinet.
Durch die Integration in die SPS bleiben alle genuinen Vorteile der Robotersteuerung erhalten. So berechnet die Robotersteuerung die Bewegungskinematik und garantiert eine hohe Bewegungsqualität. Das heißt: Das Yaskawa Know-how in Sachen exakte Bewegungsabläufe der Manipulatoren bleibt weiterhin garantiert. Vor allem bei jeder Art von Handling, wie Maschinenbestückung, Picking, Packaging, Placing, Palletizing oder auch Messen, Prüfen und Sortieren können diese Roboter sowie die dazugehörige Steuerung ihre vollen Stärken ausspielen.
Die einfache Integration der Robotersteuerung in die SPS zahlt sich nicht nur beim Betrieb komplexer Produktionsanlagen aus. Mit MotoLogix genügen SPS-Kenntnisse zur Steuerung von Robotern. Somit entfällt die Suche nach robotergeschultem Personal beziehungsweise der Aufwand, um das Personal darauf umzuschulen. Das bestätigt auch David Kleinig, der das Steuerungskonzept maßgeblich realisiert hat: „MotoLogix macht es für den Endanwender, also für unsere Kunden, definitiv einfacher, in die Robotik einzusteigen. Anders gesagt: Es senkt die Hemmschwelle deutlich, wenn er sich auch bei der Bedienung und Programmierung des Roboters mit der Software weiter in der SPS-Welt bewegen kann, in der er sich schon auskennt.