Kommentar : Anforderungen zur seriellen Kommunikation gehören ins Lastenheft
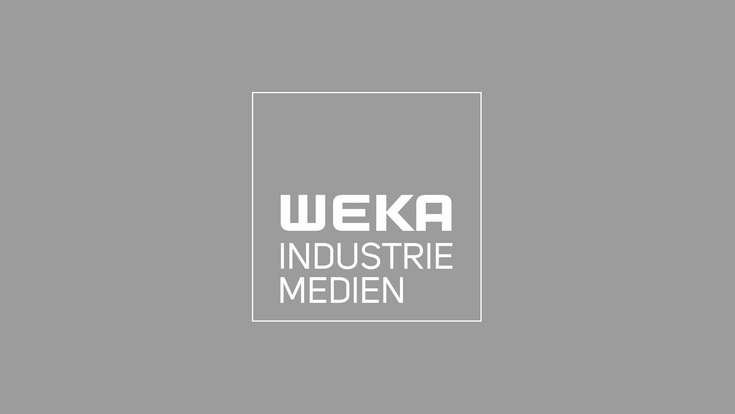
Seit Einzug der, vornehmlich elektronischen, Automatisierungstechnik in Maschinen und Anlagen, ist deren Bedeutung derart gestiegen, dass es heute kaum noch ohne geht. Dabei verschmelzen Mechanik und Elektronik immer fester zu Mechatronik und zahlreiche technologische Funktionen werden allein durch Automatisierungstechnik bzw. Software definiert oder sind dadurch überhaupt erst möglich. Entsprechend hoch sind die Anforderungen an ein Automatisierungssystem. In gleichem Maße groß, dynamisch, aber auch unübersichtlich stellt sich die Marktlage für die einzelnen Komponenten dar. Eine diffuse Gemengelage an alt Bewährtem, notwendigem Neuen und irgendwann Kommendem, macht es für Berufspraktiker und zukünftige Ingenieure immer schwerer, sich auf dem Markt zurechtzufinden.
Die Auswahl der, für die jeweilige Anwendung geeigneten, Komponenten nach technologischen, konstruktiven sowie wirtschaftlichen Aspekten und deren Konfiguration zu einem Gesamtsystem, kann daher mit erheblichem Aufwand verbunden sein, birgt reichlich Potential für Fehlentscheidungen und kann den wirtschaftlichen Erfolg eines Projektes entscheidend beeinflussen. Um diesem Sachverhalt wirkungsvoll zu begegnen, bedarf es einer strukturierten Methodik, an deren Anfang der Entwurf eines exzellent recherchierten Lastenheftes steht.
Lastenheft: sinnvolle Kombination aus Anforderungen und Freiräumen
Die Recherche startet üblicherweise mit der Analyse der Anforderungen und zwar beginnend beim Endprodukt, bzw. dem, was das Produktionssystem (eine Maschine oder Anlage) leisten soll. Wird diese Arbeit mit den Sichten auf die geplante Investition des Auftraggebers, den Gegebenheiten am zukünftigen Standort des Produktionssystems (dem Verwendungsumfeld) und den firmeneigenen Ressourcen des Betreibers weitergeführt, kann das Lastenheft umfassend erstellt werden (Bild 1).
Welche Anforderungen in das Lastenhaft aufgenommen werden, liegt ganz im Ermessen des Auftraggebers. Eine Orientierung an der VDI/VDE-Richtlinie 3694 ist dabei hilfreich. In [1] wurde diese Richtlinie auch für den Maschinenbau weiter entwickelt und eignet sich somit als Leitlinie für die Lastenhefterstellung von Automatisierungssystemen nahezu aller Produktionssysteme. Wichtig ist dabei, diese Leitlinien nicht als Dogma, sondern als das zu verstehen, was sie darstellen: eine Empfehlung und Orientierung. So kann es beispielsweise in Migrationsprojekten wichtig sein, die Vorgaben so genau als möglich zu definieren. Nur so kann der Projektant davon ausgehen, exakt passfähige Pflichtenhefte als Angebote zu erhalten. Andererseits können zu viele Vorgaben dazu führen, dass Anbieter kein eigenes Knowhow oder neue Technologien einbringen können. Das ist besonders bei der Neuentwicklung von Produktionssystemen zu beachten, um den Anbietern oder auch der eigenen Entwicklungsabteilung Freiräume für Innovationen einzuräumen.
Pflichtenheft: konstruktives, technologisches und wirtschaftliches Optimum
Prinzipiell gilt, dass die ermittelten Anforderungen des technologischen Prozesses in ein Lösungskonzept übertragen werden müssen. Dieses muss schlussendlich in technologischer, konstruktiver und wirtschaftlicher Sicht den gestellten Anforderungen entsprechen.
Wie in Bild 2 gezeigt, wird es in einem solchen Konzept im ersten Schritt kaum eine vollständige Überdeckung mit den Vorgaben aus dem Lastenheft geben. Es wird jedoch deutlich, dass es die Aufgabe der Entwickler ist, die resultierende Schnittmenge in einem iterativen Prozess immer größer werden zu lassen, so dass am Ende alle Anforderungen des Lastenheftes weitestgehend erfüllt werden.
Diese Optimierung muss prinzipiell für jede einzelne Komponente und mit Sicht auf das Gesamtsystem umfassend geführt werden. Dazu bieten sich zwei Perspektiven an (Bild 3). Das ist einerseits der Engineering Prozess, unter dem die Projektierungsleistung im Allgemeinen verstanden wird und der prinzipiell alle Ingenieurleistungen einbezieht. In diesem Kontext hat sich auch der Begriff Systems Engineering etabliert, worunter ein nachhaltiger Entwicklungsprozess mit Blick über den gesamten Lebenszyklus eines Produktionssystems verstanden wird.
Demgegenüber steht das Controlling, in dem alle wirtschaftlichen Aspekte berücksichtigt werden. Dazu gehört die Projektplanung, -budgetierung und -steuerung sowie die Kontrolle des Projektablaufes. Grundsätzlich gilt, dass die Bearbeitung in den einzelnen Sichten naturgemäß nicht singulär und isoliert voneinander erfolgt. Vielmehr ist es wieder eine gewerkeübergreifende Teamarbeit, in der es einen ständigen Austausch an Aufgaben und Informationen gibt.
Das Automatisierungssystem erfordert besondere Beachtung
Moderne Produktionssysteme sind zunehmend hochautomatisiert, was eine besondere Sicht auf die Automatisierungstechnik verlangt. Bild 4 zeigt eine Auswahl der für die Automatisierung relevanten Kriterien, die im weiteren Entwicklungsprozess detailliert zu analysieren sind. Mit dieser Sicht muss wiederum die Auswahl jeder einzelnen Komponente des Automatisierungssystems geführt werden.
Im Fall der Kommunikation gehört dazu die Auswahl geeigneter Feldbussysteme, sowie diverser zusätzlicher (vorzugsweise serieller) Schnittstellen wie USB-, WLAN- und sonstigen Interfaces – beispielsweise IO-Link für die Kommunikation mit intelligenten Feldgeräten. Wird das Produktionssystem in ein IT-System eingebunden, sind neben der Auswahl des Mediums und der Übertragungsprotokolle auch Maßnahmen zur Datensicherheit (Security) erforderlich. Des Weiteren sind zur Integration in die digitale Produktion Industrie 4.0-konforme Protokolle entsprechend der vorgesehenen CP-Klassifikation auszuwählen. Und schließlich spielt auch die Übertragung sicherheitsgerichteter Signale im Sinne der Maschinen- und Anlagensicherheit (Safety) eine maßgebliche Rolle.
Serielle Kommunikation im industriellen Umfeld
Das Thema serielle Kommunikation ist derart vielgestaltig, dass die Entwickler genau auf die speziellen Anforderungen fokussieren müssen, die für den Entwurf ihres Automatisierungs-systems von Bedeutung sind. Dazu sollten sie sich zunächst mit den unterschiedlichen Anforderungen an den Datenverkehr im konkreten industriellen Umfeld des Produktionssystems beschäftigen, um anschließend die erforderlichen Kommunikationsverfahren für ihr Automatisierungssystem zu bewerten und auszuwählen. Grundsätzlich muss bei der Betrachtung industrieller Kommunikationssysteme zwischen den Feldbussen, ganz gleich welcher physikalischer und informationeller Ausprägung, und sogenannten Punkt zu Punkt-Schnittstellen (Point to Point, PtP) unterschieden werden. Während letztere aktuell eher für die serielle Kopplung von Feldgeräten mit IO-Komponenten verwendet werden, sind Feldbusse für die echtzeitfähige Vernetzung nahezu aller Automatisierungskomponenten und -systeme vorgesehen. Dazu sind am Markt eine Vielzahl unterschiedlicher Systeme verfügbar, deren wichtigsten Unterschiede, Stärken sowie Anwendungsvorteile zu betrachten sind.
Die Auswahl der für das Projekt geeigneten Systeme und Komponenten sollte unter Berücksichtigung der folgenden und beispielhaften Auswahlkriterien erfolgen:
Konstruktion und Investitionssicherheit
Gewährleistung einer Auf- und Abwärtskompatibilität
(Updates, Geräte unterschiedlicher oder gleicher Hersteller)
einfache industrietaugliche Infrastruktur
(Kabel, Stecker, Strukturkomponenten, Umgebungsbedingungen)
freie Wahl der Übertragungsmedien
(Kabel, Licht, Funk)
freie Wahl der Netzwerk-Topologie
(Linie, Stern, Baum)
Hotplug-Fähigkeit
(automatische Detektion und Registrierung von Teilnehmern)
Zugang zur Technologie
(Nutzerorganisation, Lizenzen)
Unterstützung durch internationale Normen
Technologie und Leistungsfähigkeit
geringstmögliche Zykluszeit
deterministisches Zeitverhalten möglichst ohne Jitter
synchroner und asynchroner Datenverkehr auch mit großen Datenmengen
mögliche Querkommunikation z.B. nach dem Producer-Consumer-Prinzip (Pub/Sub)
Möglichkeit einer Safety-Kommunikation
gesicherte Datenübertragung (Security)
Industrie 4.0-Konfirmität
Wirtschaftlichkeit
Kosten der einzelnen Komponenten
(einzelner Knoten, Infrastruktur)
Implementationsaufwand
(Entwicklung, Applikation, Inbetriebnahme)
Service und Diagnose
(Gerätetechnik, Training)
Kosten des Betriebes
(Lizenzkosten)
Welche Kommunikationsschnittstelle ist die richtige?
Trotz des Siegeszuges der Ethernet-basierten Feldbusse und nicht zuletzt durch OPC UA, speziell in Kombination mit dem Publish/Subscribe-Modell (Pub/Sub) und Time Sensitive Networking (TSN), sind dedizierte Feldbusse immer noch aktuell und gehören somit in das Portfolio jedes Herstellers von Automatisierungstechnik. Dazu gehört vor allem der Profibus, welcher in der Version PA für Prozessanlagen speziell im Ex-Bereich nach wie vor defacto Standard ist. Aber auch CAN bzw. CANopen, Interbus, Modbus oder auch branchenspezifische Varianten wie BACnet für die Gebäudeautomatisierung, werden aufgrund ihrer Verbreitung noch einige Zeit eine Rolle spielen.
Ungeachtet dessen werden zukünftige technologische Entwicklungen sowohl die Möglichkeiten, aber schlussendlich auch die Anforderungen an eine moderne und vor allem geeignete industrielle Kommunikation bestimmen. Wie die Beispiele OPC UA TSN oder die Standardisierungsaktivitäten rund um Industrie 4.0 es zeigen, sind die Entwicklungen dazu in vollem Gang.
Aktuelle und zukünftige Automatisierungslösungen müssen sich deshalb daran messen lassen, wie sie in der Lage sind, diese Entwicklungen mitzutragen bzw. durch intelligente An
sätze voranzutreiben. Hersteller, die meinen, wie bisher ihre Marktstellung durch proprietäre Einzellösungen sichern zu können, müssen umdenken oder werden auf der Strecke bleiben.
Allein aus diesem Grund sind Konstrukteure gut beraten, in aktuellen und zukünftigen Entwicklungen von Beginn an ausschließlich auf standardisierte und soweit als möglich offene Kommunikationsprotokolle und -lösungen zu setzen. Steuerungen, die auf- und abwärtskompatibel sind, mit HMI-Systemen WEB-basiert über OPC UA kommunizieren und die in der Lage sind, Datenpakete in harter Echtzeit gemeinsam mit sicherheitsrelevanten Informationen zu transportieren, sind dafür sicher der richtige Ansatz.