Flexible Automatisierung : Automatisierung in der Batterieproduktion verspricht sichere und bezahlbare Energie
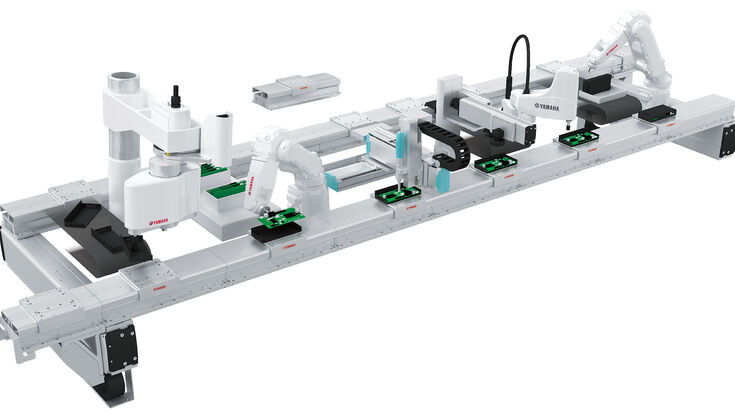
Batterien werden in Zukunft eine zentrale Rolle in der nachhaltigen Energieversorgung und Mobilität spielen. Es werden erschwingliche, qualitativ hochwertige Lithium-Batteriepakete mit verschiedenen kWh-Kapazitäten benötigt, um Fahrzeuge wie E-Bikes, Drohnen und kleine Stadtautos bis hin zu großen Elektrofahrzeugen (BEVs), Lastwagen und Bussen anzutreiben. Andererseits werden containergroße Batterie-Arrays als Energiespeicher für private, gewerbliche und versorgungstechnische Anwendungen benötigt, um die Stabilität der grünen Stromnetze von morgen zu gewährleisten.
Batterieangebot und -nachfrage
Dank frühzeitiger Investitionen und Planungen haben sich Korea und China zu den heute führenden Standorten für die Batterieherstellung entwickelt. China ist der weltweit größte Hersteller von Lithium-Ionen-Batterien, auf den etwa 80 % der weltweiten Produktion entfallen. Das Beratungsunternehmen McKinsey & Company geht davon aus, dass die gesamte chinesische Produktionskapazität bis 2025 etwa 1220 GWh betragen wird.
Da die westlichen Regierungen begonnen haben, den Übergang von der Mobilität mit fossilen Brennstoffen zu E-Fahrzeugen zu planen, um die im Pariser Abkommen
festgelegten Umweltziele zu erreichen, werden lokale Kapazitäten für die Batterieherstellung benötigt. Dementsprechend nimmt die Kapazität zur Herstellung von Lithiumbatterien in Europa zu, da sich einheimische Hersteller und ausländische Investoren darauf vorbereiten, die Nachfrage zu bedienen. Es wurden Pläne für neue Fabriken und die Erweiterung bestehender Anlagen angekündigt, die die Kapazität zur Herstellung von Lithium-Ionen-Batterien bis 2025 auf fast 500 GWh und bis 2030 auf fast 800 GWh steigern könnten.
Batteriepacks für den Automobil-, E-Mobilitäts- und Allzweckmarkt können mit zylindrischen Zellen in Standardgrößen wie dem Formfaktor 18650 (18 mm Durchmesser, 65 mm Länge) oder mit Flachzellen in Standard- oder kundenspezifischen Größen gebaut werden. Bei einer Flachzelle kann es sich um eine prismatische Zelle handeln (die in der Regel in einem quadratischen, geschweißten Aluminiumgehäuse untergebracht ist) oder um eine flexible Pouch-Zelle. Während zylindrische Zellen von einer hohen Festigkeit und Langlebigkeit profitieren, können flache Zellen den Platz im Akkupack effizienter nutzen. Pouch-Zellen, die kein Metallgehäuse haben, sind am platzsparendsten und leichtesten, allerdings ist in der Regel eine zusätzliche mechanische Verstärkung innerhalb des Batteriepacks erforderlich.
Sichere und wirtschaftliche Batterien produzieren
Bei beiden Zellentypen beginnt die Herstellung mit der Vorbereitung und dem Aufbringen aktiver und leitender Beschichtungen auf die Elektrodenblätter und dem Laminieren der Blätter. Präzision und Wiederholgenauigkeit sind äußerst wichtig, um die Konsistenz von Merkmalen wie Beschichtungszusammensetzung und -dicke zu gewährleisten. Die exakte Übereinstimmung der Zellenparameter innerhalb der Batterie trägt so zur Sicherheit und Langlebigkeit bei.
Schnelligkeit und Effizienz sind ebenfalls von entscheidender Bedeutung, insbesondere bei der Bedienung von Märkten wie der Automobilindustrie, die sehr preissensitiv ist. Reichweitenbedenken und Erschwinglichkeit sind zwei Schlüsselfaktoren, die die breite Akzeptanz von E-Fahrzeugen beeinflussen. Die Batterie hat einen entscheidenden Einfluss auf beide Faktoren. Eine Erhöhung der Batteriekapazität bedeutet eine größere Reichweite, aber auch höhere Fahrzeugkosten. Die Kostengleichheit mit Fahrzeugen mit herkömmlichem Verbrennungsmotor wird für das Jahr 2025 erwartet, und der Verkauf von Neufahrzeugen mit Verbrennungsmotor dürfte in den wichtigsten westlichen Märkten und in China ab etwa 2030 eingestellt werden. Die Hersteller müssen die Kosten der Batterien für Elektrofahrzeuge senken. Skalierungseffekte werden sicherlich hilfreich sein, aber auch die Maximierung der Produktivität in der Fertigung ist von entscheidender Bedeutung, wenn nach dem Verbot des Verbrennungsmotors weiterhin viele Menschen ein Auto besitzen wollen.
Die Automatisierung ist der Schlüssel zum Erreichen der Geschwindigkeit und Wiederholgenauigkeit, die für die Gewährleistung von Zuverlässigkeit und Wirtschaftlichkeit erforderlich sind. Für Prozesse wie die Vorbereitung und das Auftragen von Beschichtungen auf Elektrodenfolien, das Laminieren der Folien, das Schneiden in Streifen und das Anbringen von Elektroden durch Schweißen werden häufig kundenspezifisch automatisierte Anlagen eingesetzt.
Zum Bau einer zylindrischen Zelle werden die Streifen zu einem Zellkern mit Anode, Separator und Kathode gewickelt, der dann in das zylindrische Gehäuse eingesetzt wird. Das Gehäuse ist gerillt, um den Kern zu fixieren, mit Elektrolyt gefüllt, abgedichtet und mit externen Kontakten versehen. Flachzellen werden in einer ähnlichen Verfahrensabfolge hergestellt, einschließlich des Stapelns der Elektrodenschichten, des Verschweißens des prismatischen Gehäuses oder des Formens und Abdichtens des Pouch mit Hilfe von Heißsiegel- und Vakuumversiegelungsverfahren. Die Zellen und Batteriepacks werden einer elektrischen Prüfung und einer automatischen Röntgenprüfung unterzogen, um ihre Leistung und Funktionsfähigkeit sicherzustellen.
Flexible Automatisierung
Die Einführung von Robotern in den Fertigungsablauf bietet Vorteile wie kurze Zykluszeiten und einen präzisen, wiederholgenauen Betrieb. Außerdem wird die Systemintegration durch den Einsatz programmierbarer Standardroboter beschleunigt. Weitere Vorteile sind die einfache Skalierbarkeit und die Flexibilität, das Fabriklayout und die Montageprozesse an die sich ändernden Markt- und Kundenanforderungen schnell anzupassen.
Yamaha hat seine Roboter an Batteriehersteller in ganz China und Korea geliefert, den Zentren der größten und erfolgreichsten Batteriehersteller. Die Roboter übernehmen ausgewählte Prozesse im Fertigungsablauf. In der Tat werden in China derzeit mehr als 3000 SCARA-Roboter in der Batterieproduktion eingesetzt. Diese werden in großem Umfang zum Be- und Entladen von Materialien, Bauteilen und teilweise fertigen Baugruppen verwendet, wenn die Batterien von einem automatisierten Fertigungsprozess zum nächsten wechseln.
Voraussetzung für diese Be- und Entladevorgänge sind natürlich Genauigkeit und hohe Geschwindigkeit. Das Gleiche gilt für Wiederholgenauigkeit und Zuverlässigkeit. Aufgrund der hohen Marktnachfrage läuft die Produktion in der Regel 24 Stunden am Tag, sieben Tage die Woche. Große Batteriehersteller haben sich für diese Anwendungen für Yamahas SCARA-Roboter YKXG entschieden (Bild 1). Ihr leistungsstarker, riemenloser Antriebsmechanismus mit Motoren mit vertikaler Welle und direkt angetriebener Kugelumlaufspindel ermöglicht einen kontinuierlichen Betrieb über längere Zeiträume mit gleichbleibender Genauigkeit. Vergeudete Bewegungszeit sowie Verschleiß und Bruchgefahr, wie sie bei herkömmlichen riemengetriebenen Alternativen auftreten, entfallen ebenfalls. Der wartungsfreie riemenlose Antrieb senkt zudem die Betriebskosten.
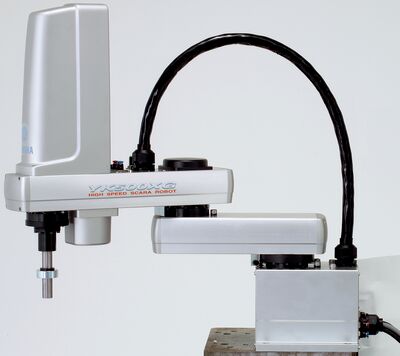
Die allgemeine Einführung von Elektrofahrzeugen hat zu einer starken Nachfrage nach einer größeren Reichweite geführt. Im Gegenzug verlangen die Automobilhersteller nach immer leistungsfähigeren Batterien. Die YKXG-Serie wurde entwickelt, um diesem Trend Rechnung zu tragen, und bietet eine maximale Nutzlast von bis zu 20 kg für die Handhabung großer Pouch-Zellen und teilfertiger Batteriebaugruppen. Die spezielle R-Achsen-Konstruktion von Yamaha ermöglicht ein hohes Masseträgheitsmoment der Last, was den Roboter in die Lage versetzt, schwere Teile zu handhaben, die Beschleunigung und Abbremsung zu maximieren und die Stabilität aufrechtzuerhalten, was letztlich eine kurze Zykluszeit gewährleistet.
Kartesische Roboter werden auch häufig für Dichtungsprozesse bei der Montage von quadratischen Batteriezellen eingesetzt. Langlebigkeit und Zuverlässigkeit sind für die Aufrechterhaltung der Produktivität von großer Bedeutung. Die kartesischen Roboter von Yamaha enthalten Resolver zur Positionserfassung, die weder elektronische Bauteile noch optische Elemente enthalten und daher nicht durch Fett oder Staub aus der Fabrik verunreinigt werden können. Daher sind sie äußerst zuverlässig und gleichbleibend genau. Darüber hinaus profitieren die Führungsschienen der kartesischen Roboter von einer Zweipunkt-Konstruktion, die die Reibung minimiert und Ausrichtungsschwankungen selbst bei der Handhabung von Lasten mit hohen Momenten verhindert.
Während einachsige Roboter häufig in Fabriken aller Art eingesetzt werden, bieten die linearen Fördermodule LCMR200 von Yamaha für Anwendungen, bei denen ein Hochgeschwindigkeitstransport von Gegenständen erforderlich ist, einen schnellen, präzisen und flexiblen lokalen Transport zwischen Prozessen und innerhalb von Montagezellen (Bild 3). In Batteriefabriken werden sie häufig für den Transport fertiger Baugruppen zur Röntgeninspektion eingesetzt. Da die einzelnen LCMR200-Module präzise miteinander verknüpft und koordiniert werden können, wird jeweils ein Modul auf beiden Seiten der Schutztür am Eingang des Röntgengeräts installiert, um die Baugruppen in den Inspektionsprozess zu transportieren und die Sicherheit der Bediener in der Nähe zu gewährleisten.
Insgesamt sind mehr als 80 % der Prozesse bei der Herstellung der heutigen Hochleistungs-Lithiumbatterien automatisiert, wobei eine Kombination aus herkömmlicher Fabrikautomation und flexiblen, programmierbaren Robotern eingesetzt wird, die zusammenarbeiten, um Qualität und Produktivität zu maximieren.
Yamaha setzt seine umfassenden Erfahrungen aus ganz Asien – unter anderem in der Zusammenarbeit mit führenden Batterieherstellern und Systemintegratoren – nun auch in Europa ein, um hier die Expansion der hochmodernen Batterieproduktion zu unterstützen.
Der Einsatz von Robotern zur Automatisierung ausgewählter Aspekte der Batteriemontage ermöglicht es Herstellern, Batterien nach genauen Spezifikationen und unter Einhaltung enger Kostenvorgaben herzustellen. Ihre Unterstützung für Hochgeschwindigkeits- und Qualitätsmontage geht einher mit Flexibilität und Skalierbarkeit. Roboter, die über einzigartige Merkmale zur Verbesserung von Präzision und Langlebigkeit verfügen und sich in den führenden Batterieherstellungsregionen bewährt haben, können dazu beitragen, ein reichhaltiges Angebot an kostengünstigen Batterien sicherzustellen, um die wachsende Nachfrage auf den verschiedenen Märkten weltweit zu bedienen.
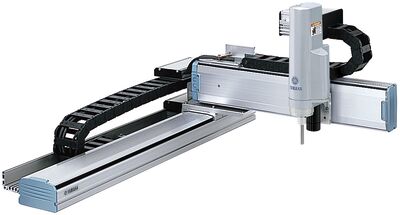